PET Preform Moulds and Preform Molds: Innovating the Packaging Industry
Jul 10,2023
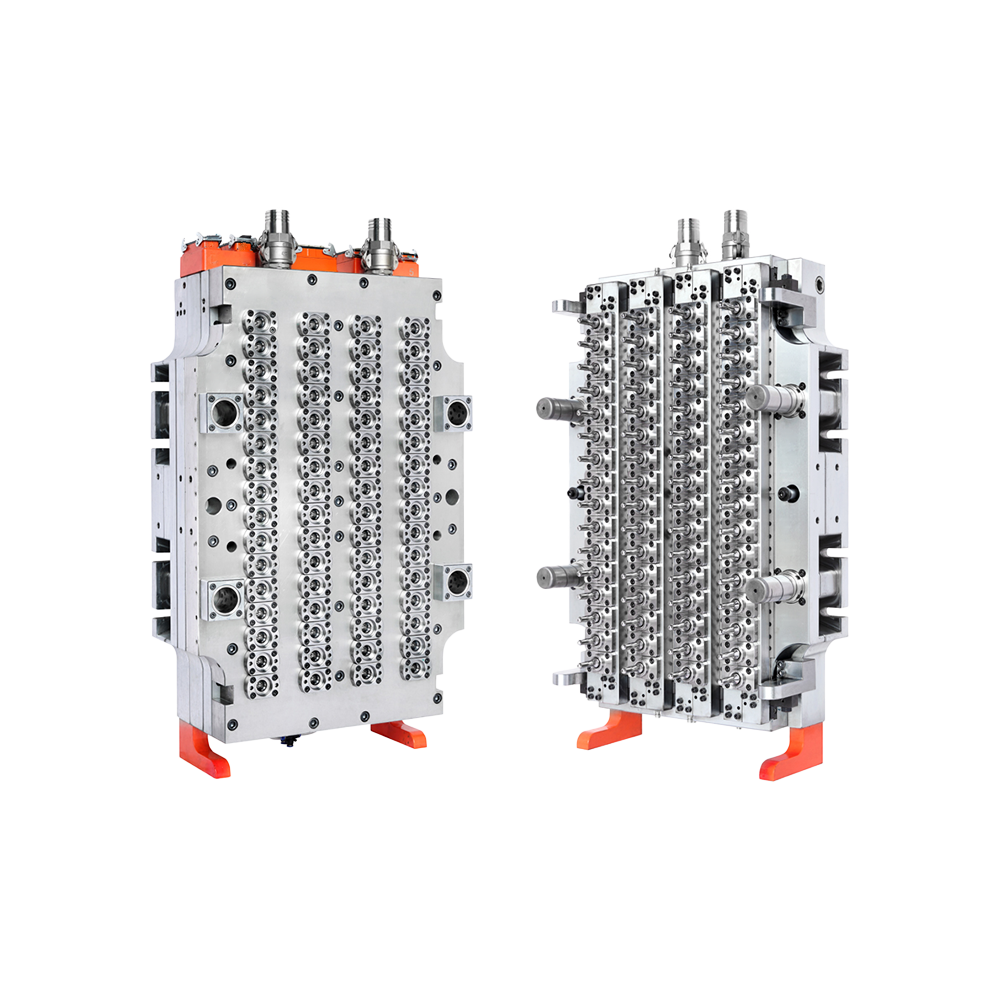
In recent years, PET (Polyethylene Terephthalate) preform moulds and preform molds have revolutionized the packaging industry. With their efficient manufacturing process and versatile design capabilities, these molds have become integral in the production of PET bottles. This article will delve into the intricacies of PET preform moulds and preform molds, exploring their manufacturing process, advantages, and significant impact on the packaging industry.
Manufacturing Process of PET Preform Moulds and Preform Molds:PET preform moulds and preform molds are expertly constructed using high-quality steel. The manufacturing process involves several crucial steps, including mold design, material selection, machining, and surface treatment. Advanced techniques such as computer-aided design (CAD) and computer numerical control (CNC) machines are employed to create precise and intricate mold designs.
Advantages of PET Preform Moulds and Preform Molds: Efficient Production: PET preform molds enable manufacturers to produce PET bottles in large quantities with high efficiency. The injection molding process allows for swift production cycles, reducing the time required for cooling and solidification.Cost-effectiveness: PET preform moulds offer cost-saving advantages compared to traditional manufacturing methods. The automated process eliminates extensive manual labor, minimizes material waste, and optimizes energy consumption, resulting in reduced production costs per unit.
Design Flexibility: PET preform moulds provide versatility in bottle design. Manufacturers can create bottles of various shapes, sizes, and neck finishes, catering to the unique branding and functionality needs of different industries.Lightweight and Durable Bottles: PET preform molds allow for the production of lightweight PET bottles without compromising strength and durability. These bottles are ideal for packaging beverages and other liquid products.
Significant Impact on the Packaging Industry: Increased Production Capacities: PET preform molds have significantly boosted production capacities, supporting the growing demand for PET bottles across industries such as beverages, cosmetics, and household products. The high-speed production capabilities of these molds cater to high-volume requirements.
Sustainable Packaging Solutions: PET preform moulds contribute to sustainability efforts within the packaging industry. PET bottles have a relatively lower carbon footprint compared to alternatives like glass or aluminum. Moreover, PET is easily recyclable, and lightweight PET bottles reduce transportation emissions.
Enhanced Product Safety and Hygiene: PET preform moulds produce bottles with consistent wall thickness and dimensional accuracy, ensuring tight seals and preventing leaks or contamination. These bottles are widely trusted for the safe storage of food, beverages, and personal care products.
Innovations in Bottle Design: PET preform molds have spurred innovations in bottle aesthetics and functionality. Complex shapes, embossed designs, and ergonomic features are now achievable, helping brands differentiate their products and attract consumers.
Future Developments:
As technology advances, PET preform moulds and preform molds will continue to evolve, bringing further improvements to the packaging industry:Integration of Robotics and Automation: Automation and robotics will streamline the manufacturing process, enhancing efficiency, and reducing production costs.Enhanced Material Properties: Research and development efforts are focused on improving the material properties of PET bottles, enabling them to withstand changing market demands and enhance their overall sustainability.
Conclusion:PET preform moulds and preform moulds are catalysts in transforming the packaging industry. Their efficient production and cost-saving benefits have revolutionized PET bottle manufacturing, while also promoting sustainability and meeting the demands of diverse industries. With continuous technological advancements and a focus on innovation, these moulds will continue to play a pivotal role in shaping the future of the packaging industry, meeting consumer demands, and driving sustainable practices.