28mm 28g Preform Mould: The Backbone of Plastic Bottle Manufacturing
Aug 21,2023
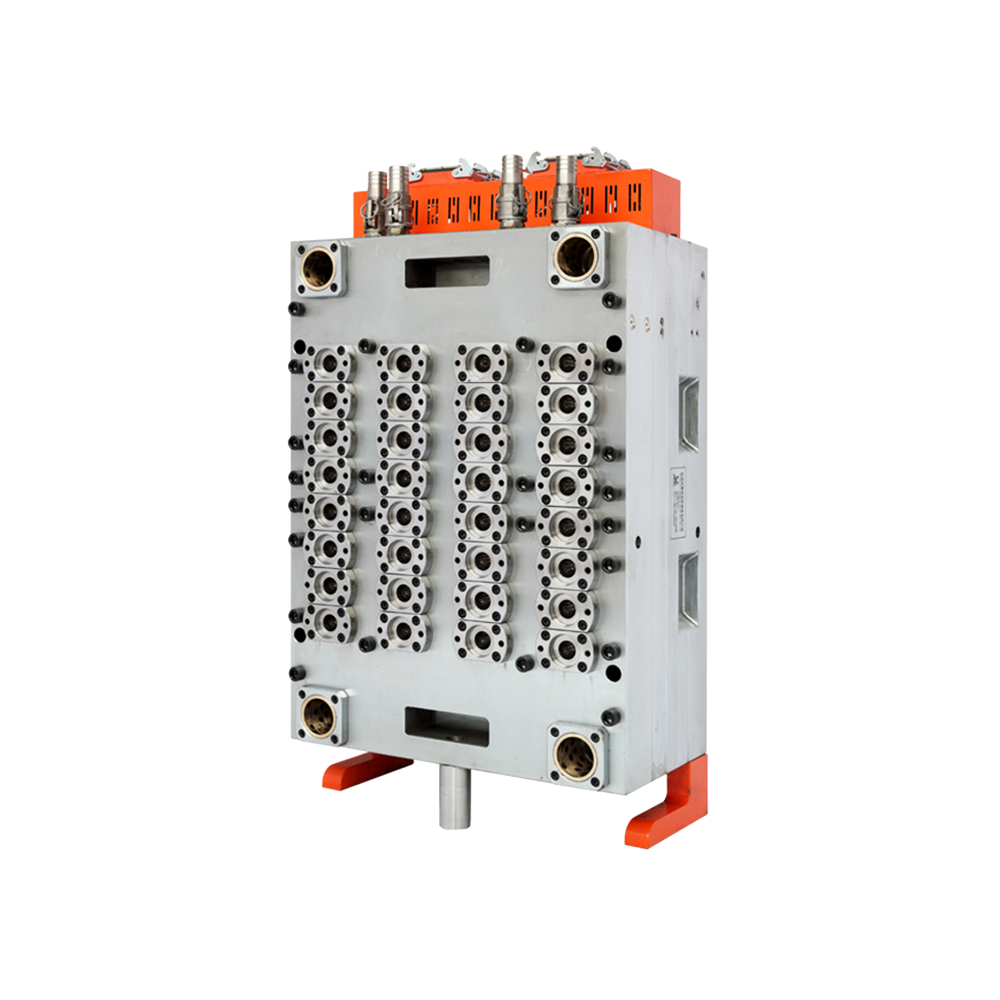
In the world of manufacturing, attention is often diverted towards the final products that consumers see on the shelves. However, the complex processes and tools behind their creation are often overlooked. One such tool of paramount importance in the world of plastic bottle manufacturing is the 28mm 28g Preform Mould.
A preform mould, specifically, a 28mm 28g preform mould, is a precision tool used in the injection moulding process. It gives plastic bottles their initial, tube-like shape, which is subsequently blown into the final product. This initial shape, or preform, is critical as it carries the bottle's neck with the threaded portion where the cap will fix, thus defining the critical seal between the bottle and the cap.
In the world of plastic manufacturing, accuracy is key. The 28mm 28g preform mould is so named because it creates a preform with a 28mm diameter neck and weighs around 28 grams. The industry standard dimensions ensure the uniformity of bottle caps across different manufacturers and product lines.
Choosing the right preform mould is crucial as it impacts the quality, strength, and transparency of the final product. Therefore, it's not just any piece of equipment, but rather, a cornerstone of the entire operation. Efficient design and manufacturing of this mould are instrumental in driving down costs, improving product quality, and boosting the overall productivity of manufacturing. To work effectively, a 28mm 28g preform mould must be constructed with exact precision and from robust materials. Stainless steel is often the material of choice for its durability, corrosion resistance and ability to withstand high pressure and temperature.
The moulding process itself is an intricately choreographed ballet of heat and pressure. The polymer is heated until it reaches a dough-like consistency, and then it's injected under high pressure into the preform mould, which is cooled rapidly to solidify the plastic while preserving the preform shape. But the process doesn't stop there. Once the preform is removed from the mould, it undergoes the blowing process. Here, the preform is heated and then blown with high-pressure air into a blow mould, transforming it into the familiar bottle shape we use daily.
The unsung hero of this process, the 28mm 28g preform mould, is a testament to the marvels of modern manufacturing. It ensures that the millions of plastic bottles produced every day are robust, leak-proof, and consistent in size and shape.
In a time when industries are striving towards sustainable practices, manufacturers are exploring using eco-friendly materials. The 28mm 28g preform mould's adaptability to accept bioplastics is a significant step towards realizing this goal.
Despite its unassuming role, the 28mm 28g preform mould indeed dictates the narrative of the modern plastic bottle manufacturing industry. Without it, the massively complex orchestration of producing bottles that are part of our daily lives would be challenging, if not impossible, to pull off.
As consumers, we might not give a second thought to the humble bottle cap or the water bottle that we use. But every time you unscrew a cap, remember that behind that simple action lies the technical brilliance of a 28mm 28g preform mould, working silently to uphold the standards of an industry that quenches the world's thirst. The shiny plastic bottles you casually grab in supermarkets have a fascinating backstory hitched to their creation, veiled away from the common eye's limelight. Intricately designed, painstakingly standardized, and meticulously produced, the quiet hero behind these plastic bottles' existence is the 28mm 28g preform mould.
Perform moulds are one of the plastic industry's key components. They come in various shapes and sizes, tailored to fit a myriad of diverse products we encounter daily. Yet, amongst the many, the 28mm 28g preform mould stands out. Synonymous with standard beverage bottles, this mould has become the industry's rock, catering to one of the most common consumer needs worldwide.