The role and production steps of preform bottle mould
Apr 07,2023
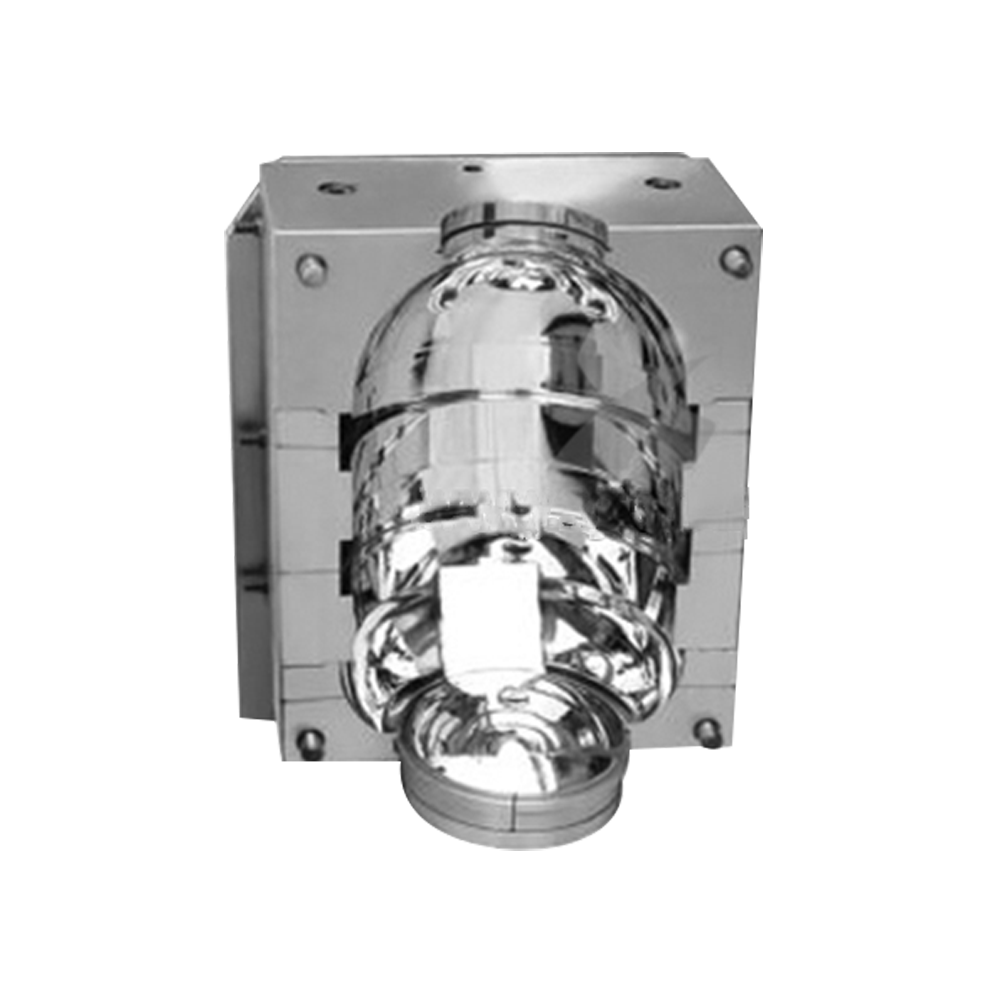
The production of preform bottle molds typically involves the following steps:Design: The mold design is created based on the specifications of the final product, such as the size, shape, and material of the preform bottle. This design is typically created using computer-aided design (CAD) software.Material selection: The material for the mold is selected based on the requirements of the production process, such as temperature resistance, durability, and cost.Machining: The mold is machined using computer numerical control (CNC) machines to create the desired shape and dimensions. This involves cutting and shaping the mold using high-precision tools.Polishing: Once the mold is machined, it is polished to ensure a smooth and even surface finish. This helps to reduce friction during the production process and prevent defects in the final product.Assembly: The mold is assembled with the necessary components, such as the core and cavity inserts, cooling system, and ejection system.Testing: The mold is tested to ensure that it meets the specifications of the final product. This typically involves running a trial production run and inspecting the preform bottles for defects or inconsistencies.Production: Once the mold has been tested and approved, it can be used for mass production of preform bottles. The mold is loaded into an injection molding machine, which melts the plastic resin and injects it into the mold to create the preform bottles.
Overall, the production of preform bottle molds requires high precision and attention to detail to ensure that the final product meets the requirements of the production process.Besides,The preform bottle mold plays a crucial role in the production of plastic preform bottles. The mold is used to shape the melted plastic resin into a specific shape and size, which will become the preform bottle. The mold consists of two halves, known as the core and cavity, which fit together to create the desired shape of the preform bottle.
The preform bottle mold determines the final shape and size of the preform bottle, including its neck, body, and bottom. It also determines the thickness and strength of the bottle walls, which are critical for ensuring that the bottle can withstand the pressure and stress of filling, transportation, and storage.The mold design also plays a key role in the production process. A well-designed mold can help to reduce production costs, increase efficiency, and improve the quality of the final product. The mold should be designed with careful consideration of the materials, production process, and final product requirements, in order to optimize production and minimize defects.
Overall, the preform bottle mold is an essential component of the plastic preform bottle production process, and plays a key role in determining the final shape, size, and quality of the product.