Unleashing Precision and Perfection: 28g Preform Molds and 30mm Preform Moulds Revolutionizing the Packaging Industry
Aug 07,2023
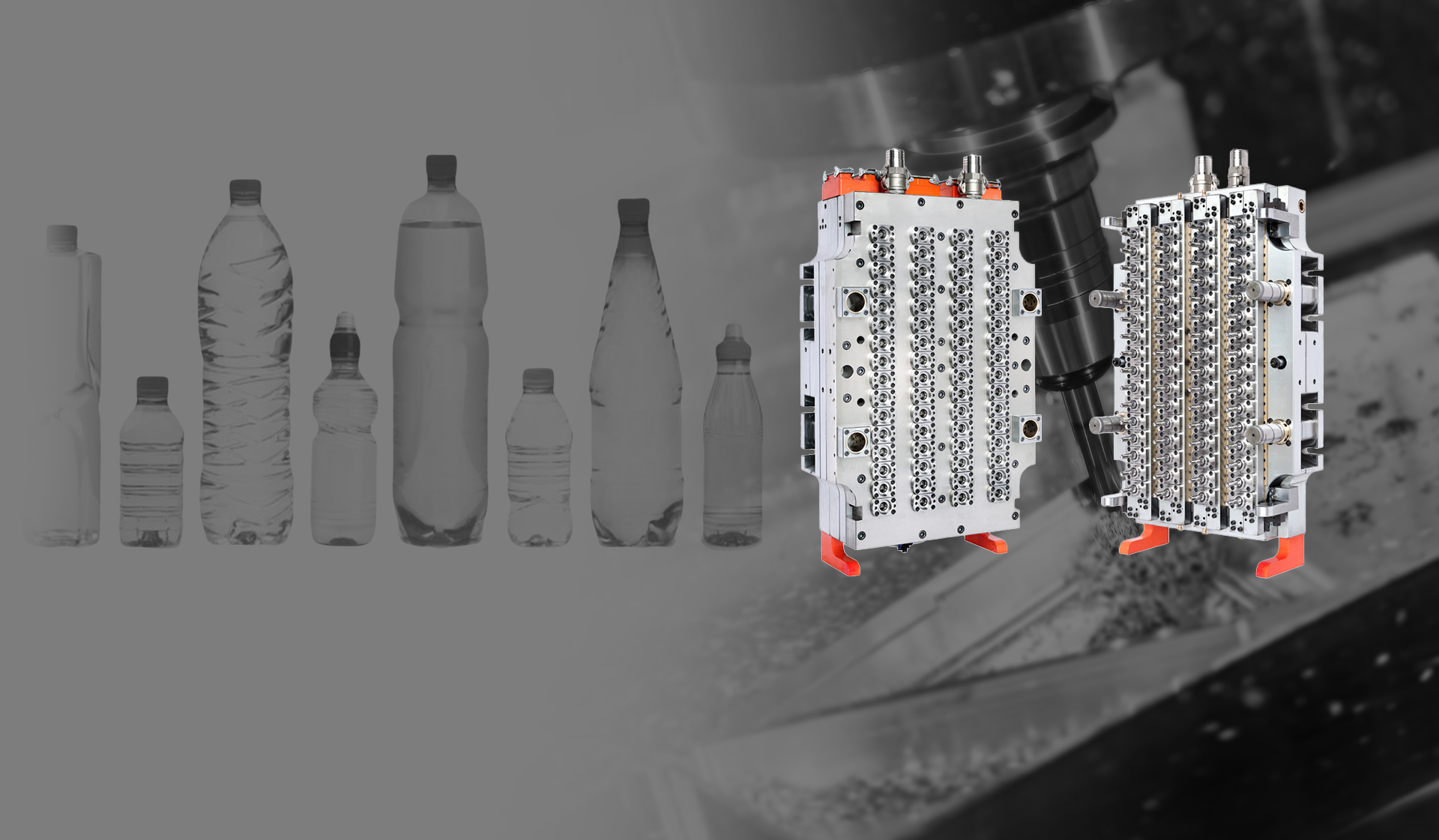
In the packaging industry, preform molds and preform molds play a crucial role in the production of high-quality and precise plastic containers. These molds are designed to create the preform, which serves as the foundation for various packaging products such as bottles and containers. The 28g preform molds and 30mm preform molds represent the cutting edge in delivering precision, accuracy, and efficiency to meet the ever-increasing demands of the industry. This article delves into the features, benefits, advancements, and applications of 28g preform molds and 30mm preform molds, illuminating their potential to redefine perfection in the packaging industry.
28g Preform Molds: Achieving Optimum Precision: The 28g preform molds provide unmatched precision in creating plastic preforms with a weight of 28 grams. These molds are designed to ensure consistency in weight, dimensions, and thickness, which are crucial for maintaining uniformity throughout the production process. The high-quality materials and precise manufacturing techniques utilized in 28g preform molds guarantee minimal variability in preform dimensions, resulting in seamless compatibility with filling and capping equipment. Manufacturers can rely on the 28g preform molds to produce preforms with accurately positioned threads, ensuring the successful closure and sealing of the final product.
Benefits and Features: The use of 28g preform molds offers significant benefits to manufacturers in the packaging industry. The precise weight and dimensions of the preforms ensure optimal material utilization, contributing to cost savings and waste reduction. The consistent design and structural integrity of the 28g preform molds prevents bottle deformities and irregularities, enhancing the overall aesthetic appeal of the final products. Additionally, the high-quality materials used in these molds, such as stainless steel or aluminum, ensure durability and resistance to wear, allowing for extended and uninterrupted production cycles.
30mm Preform Moulds: Defining Efficiency and Versatility:30mm preform molds are renowned for their versatility and capacity to produce preforms with a standardized 30mm neck finish. These molds are capable of accommodating a wide range of container sizes, shapes, and volumes, making them suitable for diverse packaging applications. The intelligent design of 30mm preform molds ensures efficient cooling and ejection, resulting in high cycle times and increased productivity. Manufacturers in various industries, including beverages, food, and personal care, rely on 30mm preform molds to produce preforms with consistent neck finishes, facilitating swift and hassle-free bottle closures.
Advancements and Technological Innovations: The packaging industry is constantly evolving, driving advancements and technological innovations in preform molds and preform molds. Manufacturers are continuously improving the design and engineering of these molds to enhance production efficiency, reduce energy consumption, and achieve more cost-effective manufacturing processes. Advancements in computer-aided design (CAD) and computer numerical control (CNC) technologies enable precise mold customization and faster turnaround times for rapid prototyping and product development. Furthermore, the integration of automation and robotics streamlines the production process, reducing human error and enhancing overall productivity.
Applications and Industry Impact: The impact of 28g preform molds and 30mm preform molds extends across multiple industries, ranging from cosmetics and pharmaceuticals to beverages and household products. These molds provide the foundation for a diverse range of packaging solutions, including bottles, jars, vials, and containers. The precision and accuracy achieved with these molds ensure compatibility with automated machinery, filling lines, and sealing processes, enabling seamless integration into existing production workflows. The standardized preform outputs from these molds facilitate efficient downstream operations, transportation, and storage, contributing to increased operational efficiency and overall supply chain optimization.
In conclusion, 28g preform molds and 30mm preform molds hold immense potential for the packaging industry, redefining precision, efficiency, and versatility. The unparalleled accuracy and uniformity achieved by these molds guarantee high-quality preforms that meet stringent industry standards. The benefits of minimized material waste, improved aesthetics, and extended durability offered by these molds drive cost savings, sustainability, and enhanced customer satisfaction. As advancements and technological innovations continue to shape the industry, 28g preform molds and 30mm preform moulds will remain indispensable tools in the pursuit of perfection and excellence in the packaging industry.